Managing odour near our transformation sites
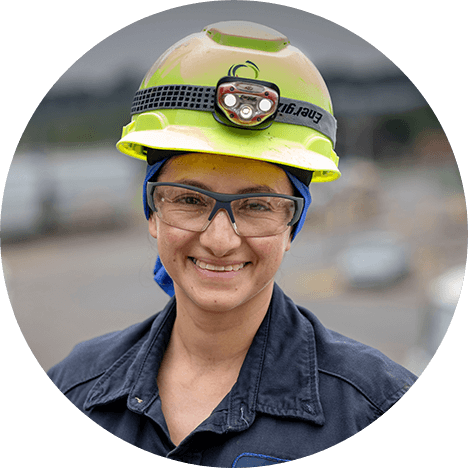
As a company specialized in rendering, Sanimax’s operations do not generate odours but rather eliminates them thanks to transformation processes. However, the transportation of organic matter to our facilities can sometimes be accompanied by odours, especially during heatwaves. We take this matter very seriously, taking concrete day-to-day measures to limit the impact of our operations on the everyday lives of those residing close to our transformation facilities.
Logistical adjustments adapted to each of our facilities along with the implementation of a state-of-the-art logistics system, the addition of processes automation, the improvement of our artificial intelligence, and targeted investments help improve the overall performance and stability of our operations. In concrete terms, these improvements allow us to deal with fewer unforeseen circumstances and thus work faster, all of which reduce the risk of odours.
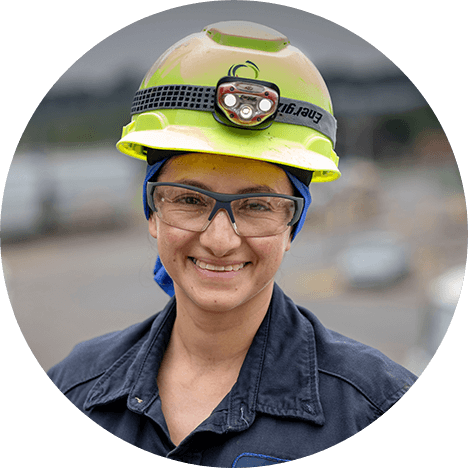
Our transformation tools for continuous improvement
Multiple factors can account for the presence of odours close to Sanimax’s transformation sites, some of which are beyond our control. Nonetheless, we continuously commission internal and external research studies in order to determine which factors potentially lead to odours and find solutions to correct the situation. Our meaningful investments toward reducing these negative effects have produced results, especially since 2019.
Our approach relies on the 3 following pillars:
Major investments to reduce odours and increase factory efficiency: increased efficiency leads to fewer delays and less odour.
Open and proactive communication with the surrounding community.
Changes in logistics and work practices, especially:
- Schedule and transportation optimization.
- Optimization approach inspired by lean manufacturing.
- Increased reliance on business intelligence and data.
Equipment modernization
- We now operate the air emission control systems on our silos and chimneys 24 hours a day, 7 days a week during the summer months.
- In 2021, we launched an air capture pilot project on a finished product silo.
- We installed an air collection system in the chicken feather processing department, identified last year as a source of odours.
- We installed an air barrier system in the feather processing department to prevent odour circulation when the door is opened.
- We operate our mist park 24 hours a day, 7 days a week during the summer months, thus neutralizing odours on-site and in neighbouring communities.
Improved operation management
Our production, maintenance and servicing schedules have been identified in the past as potential sources of odours. Indeed, technical issues can lead to processing delays, which, in turn, can generate odours. To ensure that our operations remain seamless, we have:
- Revised the management of our weekly start-up process (conducted and planned maintenance).
- Revised management practices related to plant maintenance (preventive maintenance, predictive maintenance, and more).
- Implemented artificial intelligence and automation tools (real-time reading of environmental parameters related to operations and alert systems).
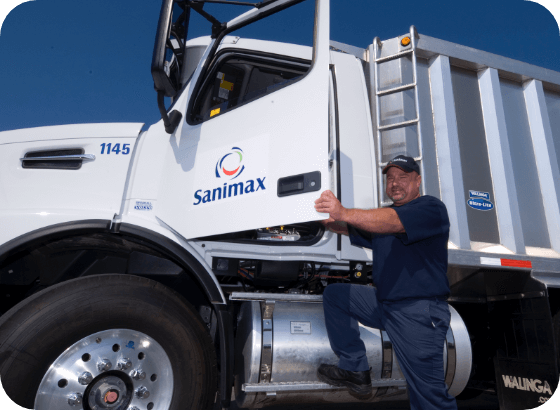
Transportation optimization
Unprocessed organic matter transported by truck to our facilities are a source of odours. For this reason, shipments must be unloaded as quickly as possible following their arrival. With this in mind, we have, through various measures, successfully reduced wait times from 8hrs in 2019 to 1,5hrs in 2020. Today, our continued efforts are backed by additional concrete actions, such as:
- Installing tarps on all Sanimax trailers at our Montréal plant
- Increasing truck maintenance (damaged tarps and potential leaks)
- Increasing the cleaning frequency of trucks and trailers
- Installing anti-spill grates on all trailers
External analysis carried out by an impartial firm
In Lévis, the warm summer of 2021 coupled with strikes in the agri-food sector has negatively impacted our transformation sites. These circumstances have prompted us to hire an external firm to assess each report.
As part of our commitment to continuous improvement, the firm in charge of assessing the situation will look at the connections between those reports and some of our operations.
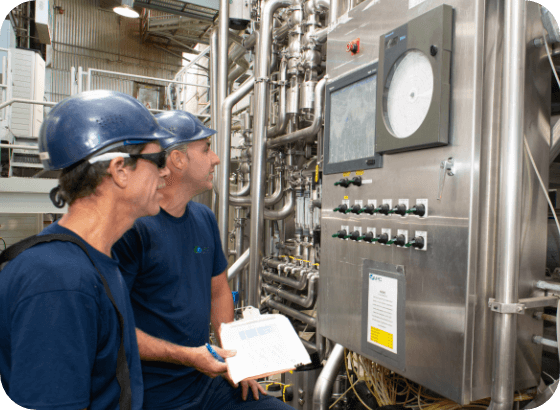
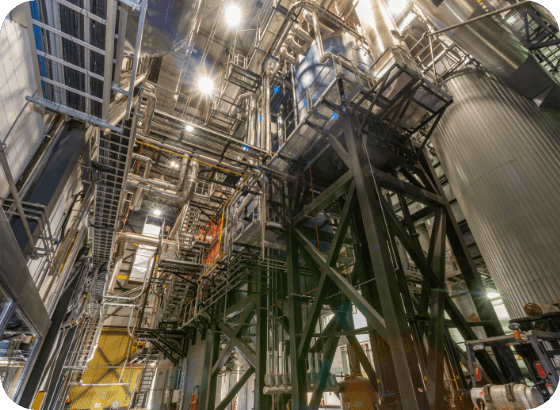
Increase the electrical robustness of our Montréal plant
By the end of 2021, we will finalize the replacement of our Montréal power substation, significantly increasing our plant’s electrical reliability.
This represents an important upgrade, as blackouts considerably impact not only our daily activities but also those of our neighbours.