An environmental mission for more than 80 years
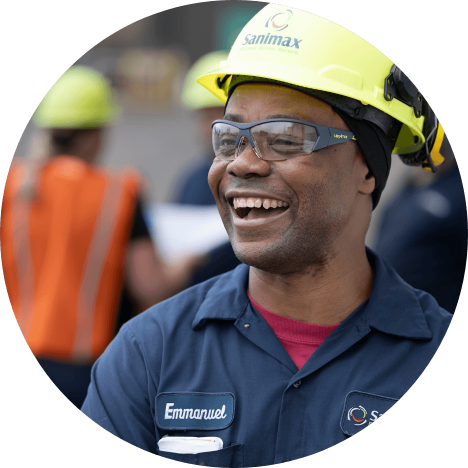
As a business that specializes in rendering, Sanimax has played a major environmental role since the moment we opened our doors. Our operations are an integral part of the circular economy, giving new life to more than 2 million tons of organic by-products every year. That’s why we call ourselves “transformation champions”!
Since our approach is based on making every effort to transform all of the materials we reclaim, we are constantly investing in our operations to make our practices and facilities increasingly eco-friendly.
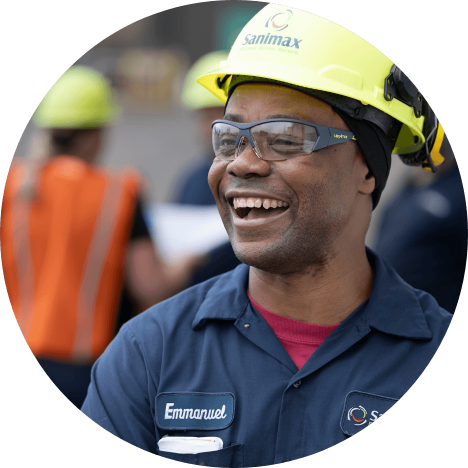
Reducing our environmental footprint
We are always looking for new ways, regardless of their size, to make our business as sustainable as possible. Here are a few examples of how we’ve optimized our commercial facilities.
Using modern biotechnology:
biofiltration and aerobic digestion to treat our wastewater and atmospheric emissions, and to return clean natural resources to the environment.
regarding odour control or renewing materials that are currently being sent to landfills.
Energy recovery and GHG emission reduction
Our Montreal facility implemented a project to recover evaporated heat from feather boilers and turn it into an energy source. This process reduces the plant’s greenhouse gas (GHG) emissions by approximately 10%.
The team also installed an Indirect Contact Condensation Economizer (ICCE) allowing heat recovery from the combustion gases that are produced by the three steam boilers. With this additional equipment, the energy recovered during the first processing stage is used to heat the water inside the deaerator and to operate an evaporation process. Then, the energy recovered during the second stage is used to heat the boiler’s makeup water and wash water. Concretely, the ICCE helps reduce GHG emissions by approximately 6%.
Innovations in biofiltration
At our Lévis plant, we developed a biofiltration process in partnership with the Centre de Recherche Industriel du Québec (Quebec Industrial Research Centre) that treats the air we release into the atmosphere. In addition to offering exceptional purification efficiency for surrounding communities and very low operational costs, this new technology helps renew a number of different by-products, including concrete residues that would otherwise be destined for landfill.
The project’s environmental and innovative nature was highlighted in 2017 when it brought home the “Industrial Environment Innovation and Protection” award at the EnviroLys Gala.
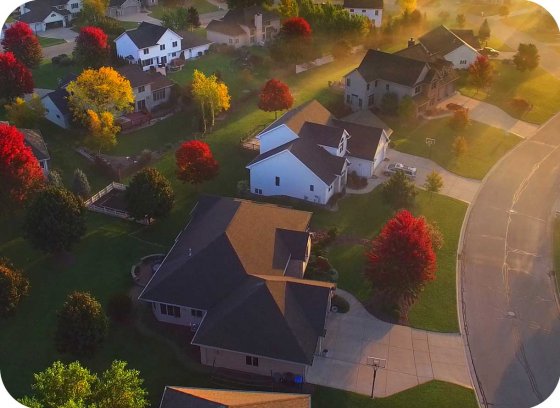
Reducing natural gas consumption
Our transformation process requires steam to operate. At our Green Bay plant, this steam is created by a boiler fueled by natural gas. In order to decrease our overall natural gas consumption, we integrated a preheating phase for the water that enters the boiler.
As a result, the amount of natural gas we have saved is equivalent to what is required to heat 1,500 residential homes for an entire year.
Reducing water consumption
We carefully analyzed our Green Bay plant’s freshwater consumption to identify areas of improvement, then modified our processes to facilitate the reuse of pumped water. These changes helped us reduce our water consumption by more than 8,250,000 gallons per year, which is equivalent to more than 10 Olympic-size pools.
These changes helped us reduce our water consumption by more than 8,250,000 gallons per year, which is equivalent to more than 10 Olympic-size pools.
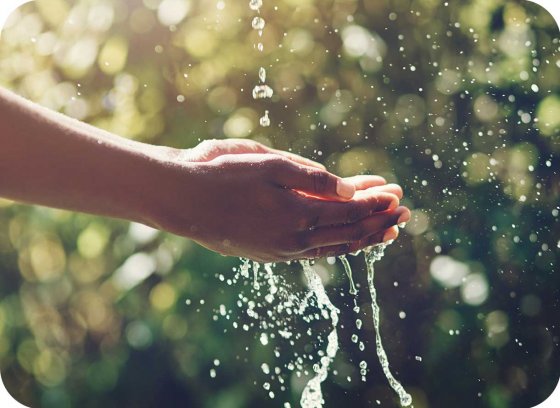
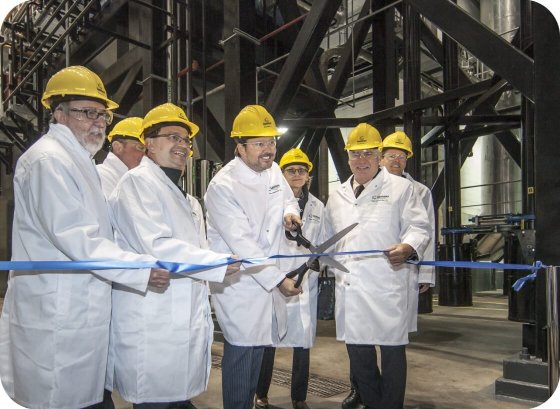
Waste reduction
Our Lévis plant is equipped with state-of-the-art equipment that helps eliminate the risk of mad cow disease. A biomass boiler removes the infectious agent via incineration. However, the treatment of resulting flue gases generates significant quantities of ash, which are then sent to landfill.
To improve our environmental performance, we upgraded our facilities to make them compatible with the use of sodium sesquicarbonate (or Trona).
These changes have reduced the quantity of ash we produce during this process by approximately 50%.
Even better, Trona has a smaller ecological footprint than the product we were using before we upgraded our equipment!